Services from Hub III: Resource-optimized electronics production
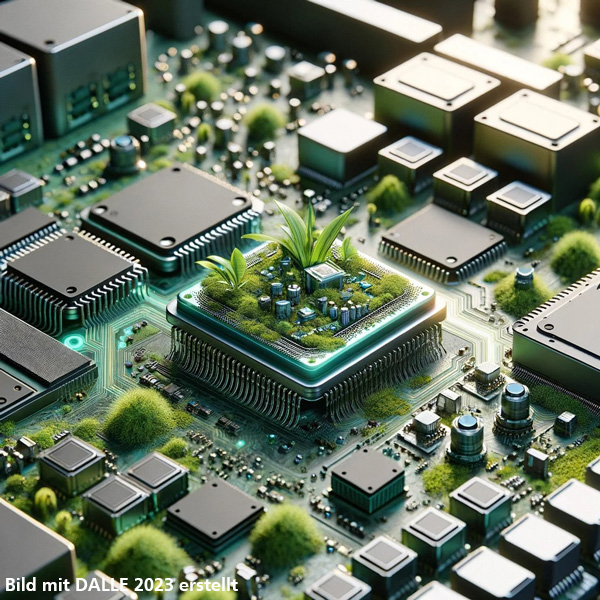
Wir untersuchen Ihre Mikroelektronikherstellung und erarbeiten Vorschläge zur Reduzierung des CO2e-Fußabdrucks. Bewerben Sie sich für ein Validierungsprojekt und lassen Sie Ihren innovativen Fertigungsprozess bis hin zum Produkt überprüfen!
Services:
- Quantification of material, resource and energy consumption to optimize manufacturing processes in cleanrooms Analysis and consulting on energy efficiency of machines and systems, including CO2 accounting
- Characterization on test structures
- Tests of alternative chemicals and processes (e.g. NMP, NF3, SF6…)
Detailed range of services: download here (pdf)
Areas examined:
- Resource-optimized microelectronic processes
- Energy-efficient cleanroom environment
- Decrease of harmful exhaust emissions
- Optimization of individual processes in terms of energy and material consumption
- Ecologically sustainable design and connection technology
- Replacement of critical materials (CMR and/or PFAS materials)
Focus topics:
- Consideration in operation: energy savings in selected scenarios
- Consideration of the resource input during production by determining the CO2e footprint (if information is available for the calculation or assessment).
- We offer to carry out a life cycle assessment for your manufacturing processes.
- The validation project's result is presented as a case study (theoretical consideration), which illustrates the savings potential through Green ICT technology. The final results are also published. Company-specific data will be treated confidentially on request.
Application form
Allgemeine Leistungen von Green ICT @ FMD:
- Know-how transfer in the creation of life cycle inventory models, life cycle assessments and calculations of the carbon footprint of products and processes
- Advice on more environmentally sustainable components and systems for sensor edge cloud applications and communication infrastructures
- More environmentally friendly manufacturing processes for microelectronic components through material substitution and energy savings in clean rooms
- Provision and plausibility checks for life cycle assessment data sets from the above-mentioned areas