Fraunhofer IPMS – N-Methyl-2-pyrrolidone (NMP) is a very effective solvent used in semiconductor manufacturing. Although it has been reported as harmful and its use is restricted, it is still necessary to find effective substitutes. Fraunhofer IPMS under the Green ICT project investigates possible replacements for NMP preserving the quality of the processes. As a starting point, IPMS works in the substitution of NMP on its own technologies. A promising stripping process was developed with an alternative solvent. Further experiments are needed to achieve the substitution in the case of lift off, balancing quality and sustainability.
Authors: Dr. Kirstin Bornhorst, Maximilian Wagner, María Esperanza Navarro Fuentes
N-Methyl-2-pyrrolidone (NMP) is a commonly used solvent in the production of microelectronics. NMP can be absorbed through the skin, inhalation, or ingestion, leading to various health effects. It is known to cause irritation and damage to the skin, eyes, and respiratory system. It also has been associated with reproductive toxicity. Making it an incredible risk for younger employees especially women. From 2020, the use of NMP is restricted under XVII of the REACH Regulation. According to this restriction, NMP is prohibited for use in concentrations equal to or greater than 0.3%.
The substitution of NMP in semiconductor production is still a challenge. It is widely used as photoresist stripper and as solvent in lift off processes. At Fraunhofer IPMS, we investigate the substitution of NMP in our clean room. The investigation is included in the Green ICT project, which focuses on a more environmentally friendly approach in semiconductor production. The substitution of critical solvents is a major topic in this project.
We use NMP as resist stripper for two different photoresists and in lift off processes with two other resists. Several candidates for the substitution of NMP were evaluated. These candidates should fulfill diverse requirements to be adequate for the quality of our processes and products. After the analysis of the characteristics of all candidates, we chose two of them to carry out experiments to determine the effectiveness and the quality of this solvent as substitute for NMP.
We measured the number of particles on clean dummy wafers after and before being coated with different resists objective for NMP substitution and removing the resists with the solvent. Then, we compared with wafers in which the resist was removed with NMP. These experiments showed good results for the stripping process for both resists with similar number of particles after NMP and the studied solvent. This solvent seems to be a good candidate to substitute NMP in our stripping processes. However, the experiments carried out until now for lift off with this solvent have not been successful. The solvent was not able to remove the resists that we used for this purpose. Thus, we need to carry out more experiments where we change the bath settings for lift off or where we consider a different substitute for NMP.
Sustainable production is necessary in order to be able to make promising developments and research at a high level of quality at IPMS. Our work on the reduction and substitution of hazardous chemicals is progressing in a good direction. Positive results have been achieved in the substitution of NMP in our clean room, but a complete substitution is still not possible and further experiments need to be carried out.
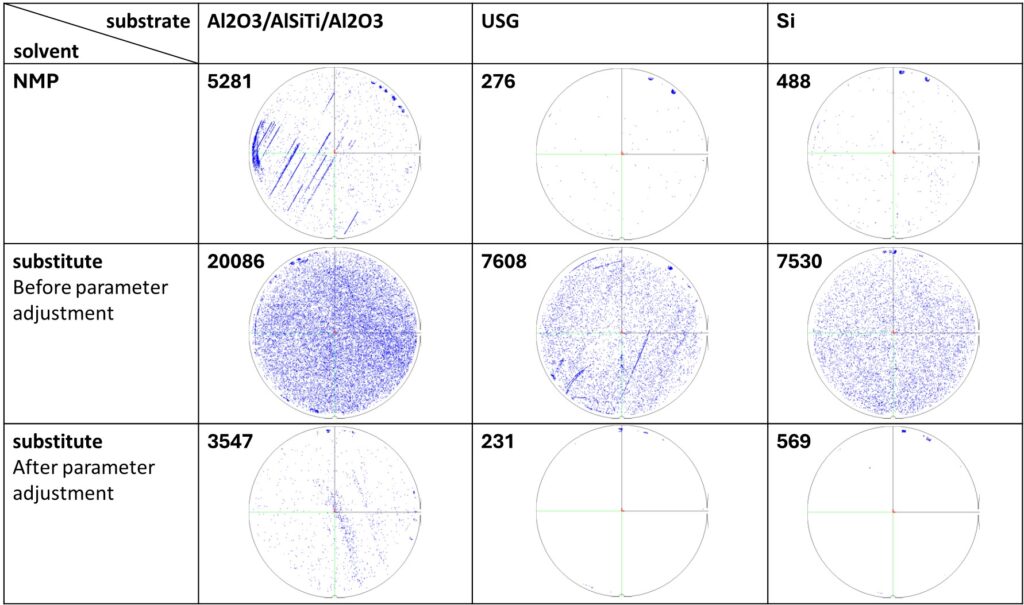
Scientific contact person:
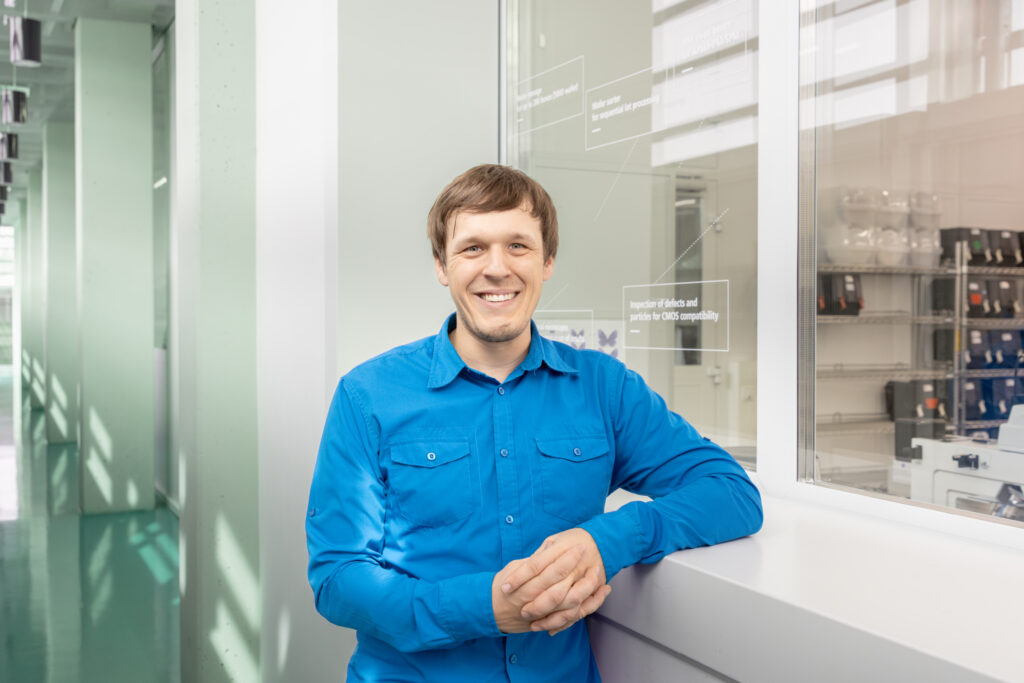
Maximilian Wagner, M.Sc.
Group Layout and Technology
Department Active Microoptical Components & Systems
Fraunhofer Institute for Photonic Microsystems IPMS
Phone: +49 351 8823-1706
maximilian.wagner@ipms.fraunhofer.de