Accurate monitoring of greenhouse gases is crucial to achieving the goals of mitigating the devastating effects of global warming. The Fraunhofer Institute EMFT has established a fully functional abatement lab to measure the emissions of the PFAS gases, NF3 and SF6 used in the semiconductor processes. At the same time, climate-friendly gas (FAN gas mixture) was used, demonstrating the potential of using gas abatement systems without burners.
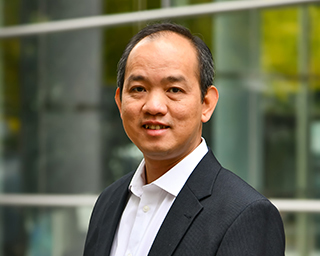
A contribution from:
Dr. Quoc Hung Nguyen
Silicon Technologies and Devices
Group Management - Structuring
Fraunhofer Institute for Electronic Microsystems and Solid State Technologies EMFT
Around 35% of greenhouse gas emissions from semiconductor manufacturing fall into the category of “direct emissions” (GHG Scope 1 for “greenhouse gases”). The contribution of process gases used and emitted in production is up to 80 percent. In the semiconductor manufacturing industry, low-molecular fluorinated gases from the group of per- and polyfluorinated alkyl compounds (PFAS, per- and polyfluoroalkyl substances) as well as NF3 and SF6 are preferably used for the deposition and structuring of thin film layers. These gases usually have a high global warming potential, which is why their climate-damaging emissions must be minimized through the use of exhaust gas purification systems (so-called abatement systems, usually consisting of a burner and scrubber). At the Fraunhofer Institute for Electronic Microsystems and Solid-State Technologies - EMFT, a research team has established a fully equipped abatement lab to measure the emission of such greenhouse gases from the plasma etching and cleaning processes with the highest possible accuracy and to reduce the emission of these harmful substances by adjusting the process parameters.
Dedicated exhaust gas measurement data from individual production facilities has shown that there are increasing inconsistencies between bottom-up and top-down methods for quantifying greenhouse gas emissions. Bottom-up estimates, i.e. measurements in factories, are sometimes only half of the global emissions estimated from atmospheric data (top-down method). Therefore, the precise determination of gas emissions at the factory level would help to further reduce the amount of pollutant gas emitted through appropriate measures and thus improve the global modeling of the emissions calculation.
Within the scope of the »Green ICT @ FMD« project, Fraunhofer EMFT has modified a PECVD (plasma enhanced chemical vapor deposition) deposition system to connect a mass spectrometer at the outlet of the process chamber in order to measure the residual gases that are emitted directly after a process. A classic propane-based burner/scrubber is used to minimize the concentration of climate-damaging exhaust gases that would otherwise be released into the air. A second mass spectrometer and an FTIR spectrometer are installed at the outlet of the burner to quantify these emitted residual gases - Fig. 1.
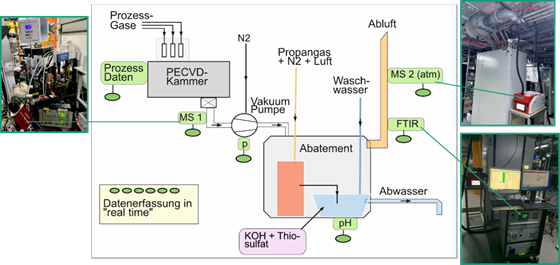
Different types of process gases are used in the PECVD system: PFAS gases, NF3, SF6 and FAN (F2/Ar/N2). FAN gas (GWP = 0) has been used at Fraunhofer EMFT for PECVD cleaning processes for years and is considered a strategic gas substitution for plasma cleaning in order to replace previously used gases with a high GWP, e.g. NF3 or PFAS gases.
In a modern, RPS-based-NF3 chamber clean process (RPS = remote plasma source), measurements with the mass spectrometer at the outlet of the PECVD chamber showed a significantly increased NF3 concentration at the end of the cleaning step. This happened after the plasma was immediately switched off, allowing the remaining pure (undecomposed) NF3 in the plasma source to flow into the vacuum pump - Fig. 2. At the outlet of the abatement system, an increase in NF3 concentration could hardly be detected, as the dilution by the burner supply air and the N2 purge gases is so high that an atmospheric mass spectrometer reaches its measurement resolution limit. Although optimizing the cleaning process can reduce the above-mentioned increase in NF3 concentration, a longer processing time per wafer is required, which results in a lower wafer throughput and ultimately higher processing costs. Only the use of FAN gas mixtures instead of NF3 will be able to completely eliminate this increased NF3 concentration.
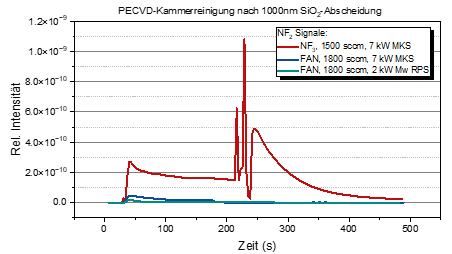
Initial measurement data with a switched-off burner (i.e. only scrubber operation without combustion with fossil propane gas) using FAN gas and the addition of thiosulphate to the scrubbing water showed no detectable HF concentrations in the exhaust gas - another option for future process control in the PECVD area with reduced harmful gas emissions.
Our Abatement Lab for the detection of fluorine-containing emissions from etching and PECVD chambers used in the manufacturing of microelectronic components is now available to interested partners from industry and business.